スポット溶接の原理
|
|
スポット溶接は、溶接したい2片の金属の上下から電極をあて、適度な圧力を加えながら、大電流を流し発生した熱で金属を溶かして接合します。
また、上下から電極を当てられないバッテリーへのタブ溶接などの場合は、左の等価回路で示したように、タブ板とバッテリー間のR3による発熱で溶接させます。溶接品質は、溶接電流・通電時間・押下圧力・材質等の影響を受けます。溶接電流は、溶接する部材の材質や表面の状態や電極押下圧力により変化します。スポット溶接により得られる接着部分を、ナゲットと呼びますが、良質なナゲットを得るためには、これらの要素をコントロールする必要があります。また、電極自身が溶着しないためには、電極の材質と放熱も重要です。同じ材質・条件下で大量・高速の溶接を行う特定用途向け溶接機が、これらを最適値に設定していくのに対して、パーソナル用は様々な素材形状と材質を相手にすることになります。でも、それほど心配はいりません。電流や電極の押下圧力、金属の導電性、金属表面の状態などは、少しの経験で、比較的簡単にコントロールできるようになります。
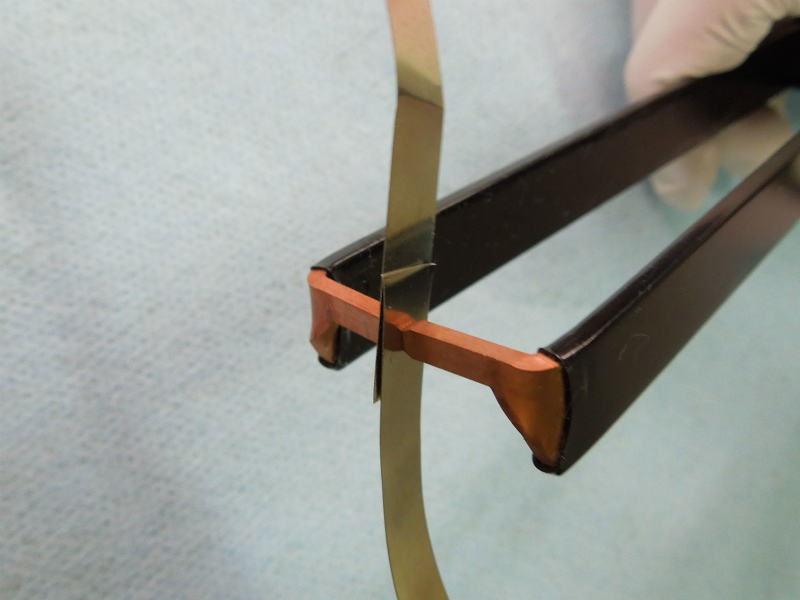 溶接ピンセットで溶接
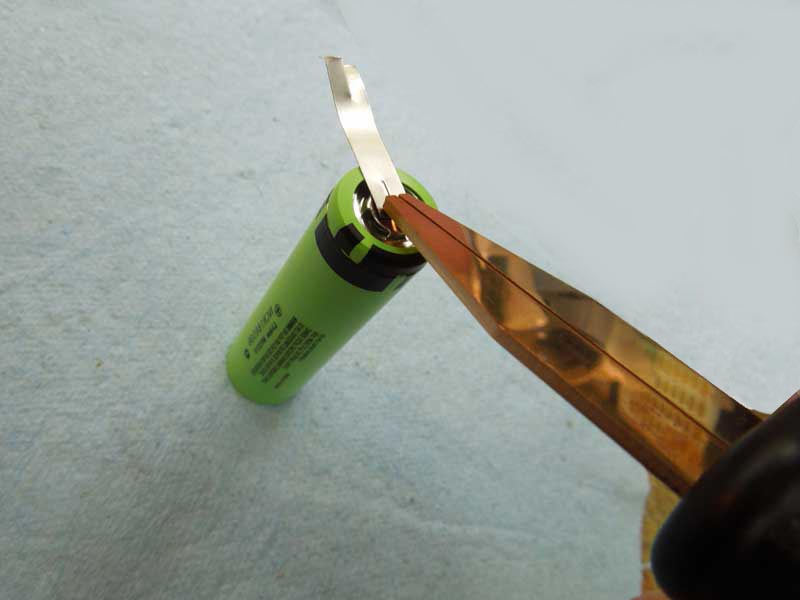
ワンハンド電極でタブ溶接
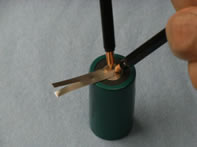
溶接ペンでタブ溶接
|
どんなものが溶接可能?
スポット溶接は、「抵抗溶接」の一種です。溶接したい物体に電気を流して、その発熱を利用して接合部の金属を溶かします。 つまり、電気を流す金属でないと溶接できません。
自動車の生産ラインで、派手な火花を飛ばして、ロボットが溶接をしているシーンをご覧になったことがあると思います。大型の溶接機であれば、どんな金属でも溶接できるかもしれません。
安全性も考慮して、加える電圧も流す電流も小さいYokodai.JP製のスポット溶接機では、細く、薄い金属しか溶接できません。
細く薄ければ溶接可能?
電気を流して発熱させるためには、その金属にある程度の抵抗が必要です。つまり、金や銀、銅、アルミニゥムなどのように電気を流しやすい金属は、発熱が少ないので、溶接しにくいのです。これらの金属は、熱伝導度も高いために、熱が逃げやすいこともスポット溶接を困難にする要因です。また、細く、薄い金属は、電流を流しすぎると、溶断してしまいますので、通電時間や電流、それに印加圧力の制御が重要になってきます。Yokodai.JP製スポット溶接機で溶接できる金属は、「Yjp機種別溶接能力」や、「金属別 溶接能力」をご覧ください。
|
ニッケルやステンレスが溶接容易な理由
|
金属の電気伝導率と熱伝導率(室温)
|
金属名 |
電気伝導率 |
熱伝導率
W/(m・k)) |
金 |
45.5 |
320 |
銀 |
61.4 |
420 |
銅 |
59.0 |
390 |
アルミニウム |
37.4 |
236 |
リン青銅 |
13~15 |
133 |
ニッケル |
14.5 |
113 |
ステンレス |
6~9 |
15~25 |
鉄 |
9.9 |
84 |
電気伝導率(導電率)の高い金属は、熱伝導率(熱伝導度)も高い。つまり、スポット溶接のために電流を流しても発熱が少ない上に熱は逃げやすいので溶接は困難です。それ故にアルミニウムや銅の溶接には、大電力が必要になります。
では、導電率が低ければ良いかというと、今度は電気が流れにくくなってしまうので、発熱もしなくなります。高電圧をかけて無理やり電流を流すことになってしまいますので、これも現実的ではありません。
|
スポット溶接は、電気抵抗による発熱を利用する溶接です。銅や銀のように電気の良導体よりも、ある程度の電気抵抗がある(電気伝導率が低い)金属のほうが溶接に適しています。
また、溶接する部分の熱が、すぐ逃げてしまう(熱伝導率が高い)ようでは、金属が溶かすことができず溶接は困難です。電気伝導率と熱伝導率は、左の表のように密接に関連しています。
従って、共に適度な値を有する、ニッケルやステンレスは、スポット溶接しやすい金属といえます。
アルミニウムは表面の酸化膜が絶縁体として働くため、溶接時には高電圧をかけてこの酸化膜を破壊する必要があります。
合金の場合は、かなり様子が異なり、銀や銅も合金となったものは、溶接が容易になる場合があります。
|
銅やアルミニウムが溶接しにくい理由 |
金属の電気抵抗率と熱伝導率(室温)
|
金属名 |
電気抵抗率 20℃
10E-8Ωm |
電気抵抗率700℃
W/(m・k)) |
融点
℃) |
熱伝導率
W/(m・k)) |
銅 |
1.69 |
6.7 |
1084 |
390 |
アルミニウム |
2.65 |
24.7 |
660 |
236 |
ニッケル |
6.99 |
|
1455 |
113 |
鉄 |
10 |
|
1535 |
84 |
ステンレス |
72 |
|
1400~1500 |
15~25 |
電気抵抗率をみると、銅は電線に使われる良導体なので電流を流しても発熱が少ないのですが、700℃になればニッケルとほぼ同じ抵抗になるので、700℃まで温度を上げることができれば溶接できそうです。しかし、熱伝導率は高いために熱は逃げやすいので厚いものは溶接は難しそうです。
アルミニウムも銅に似て電気抵抗が低く、熱伝導率が高いのでスポット溶接しにくいのですが、融点が低いため、銅よりはかなり溶接しやすいのです。
【参考文献】
http://shige.edu.yamaguchi- u.ac.jp/denkiteikou_uchita. pdf
http://www.nikkin-flux. co.jp/technology/up_img/ 1338425712-232811.pdf
http://www.morimatsu.jp/ data/stainless.html
http://www.hakko.co.jp/qa/ qakit/html/h01100.htm
|
【溶接するための工夫】
スポット溶接機を溶接容量の大きなものにするという選択肢はここではさておき、選択する材料から解決方法を探ってみます。
まず、アルミニウムですが、アルミニウムにニッケルを併せてたAl-Niクラッド材を選択する事により、ニッケルが発熱しアルミを加熱すると容易に電気抵抗率が上昇しアルミも発熱するようになりますので、容易に溶接可能となります。
銅も同じように銅にニッケルを併せたクラッド材を利用することでスポット溶接の幅が広がりますが、 Cu-Ni-Cu クラッド材は、ニッケル板よりも電気抵抗が低い配線材を使いたいというニーズから選択されています。 |
線材形状がスポット溶接しやすい理由 |
プロジェクション溶接の説明
|

 |
|
あらかじめ板材にプレス等で突起を作ります。 |
|
|
点接触による、熱集中のため小電流でも、溶融が始まり次第に広がります。 |
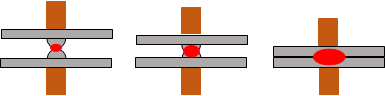 |
|
クロスワイヤ溶接の説明 |
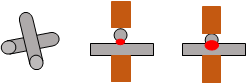 |
線材を交叉させた場合も点接触の状態から溶接が始まります |
|
線材を平行にした場合は、線接触になりますが、点接触に次ぐ効果が期待できます。 |
 |
線材を交叉させた溶接をクロスワイヤ溶接とも呼びます |
|
スポット溶接にはプロジェクション溶接と呼ばれている溶接方法が含まれます。板材同士を溶接する時に、一方の板材にあらかじめ突起加工を施し、ここにスポット溶接の電極をあてがって溶接する方法です。
突起を作ることにより、突起部分に電流が集中するために、突起部分が発熱溶融します。温度が上昇するに従って電気抵抗も適度に増加し、さらに発熱、温度上昇は周辺へも伝わり加圧により確実なスポット溶接ナゲットが得られます。
線材は、その形状から、まさにプロジェクション溶接と同様の効果が期待できるため、他の部材形状より溶接しやすいと言えます。
|
金属が溶接されて電極は溶接されない理由 |
|
|
何故、溶接したい金属だけが溶接され、電極は金属に溶接されないのでしょうか。
電極は高温でも溶けない金属を使用しているからでしょうか。その通りです。でも、それだけではありません。
溶接→溶ける←温度上昇 ということから考えてみると、大切な事が見えてきます。
|
|
|
【電極の溶着を防ぐ「形状」と「材質」】
電気を流しやすい金属を電極に使用すれば、電極は発熱せずその結果電極は溶けません。
電流を少なくすれば、当然、電極の温度は下がりますが、それでは溶接もうまくいきません。
電極先端で発生した熱を効率よく逃がしてやれば、電極先端の温度は上がりにくくなり、溶接電流で電極自体の発熱も少なくなります。
左のように電極の先端形状を整えることで、劇的に先端の温度は下がり、電極は、金属(ワーク)に溶着しにくくなります。 Yokodai.JP製の電極は、汎用性を考慮して、販売時は右のような状態になっていますので、ワークに合せてヤスリで整形してください。 |
<参考> 高温に耐える電極材質(右が大) ⇒ 電気銅 《 クロム銅 《 銅タングステン |
|
|
|
溶接に影響する「電極押下圧力」と「ペルチェ効果」
|
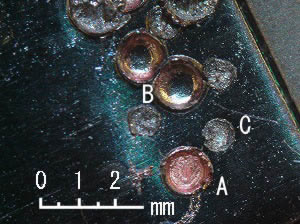
(写真クリックで拡大) |
【電極押下圧力について】
「電極押下圧力」はスポット溶接において配慮すべき重要な要素です。左の写真は0.15mm厚ステンレス板を弊社HSW-02Aで溶接した際のスポット溶接痕です。
Aは電極の銅がステンレスに溶着しています。Bは、Aと同じ条件下で、押下圧力のみ増加させて溶接した痕です。
Aは圧力不足のため電極部で発熱し、電極の銅がステンレスに溶着している様子が判ると思います。
ワークに合わせて、クロム銅電極や銅タングステン電極、銀タングステン電極などを使用することで溶着を低減できます。
|
|
【ペルチェ効果について】
ペルチェ効果とは、異なる種類の金属を接触させて電流を流すと、その金属面に熱の移動が生じる現象です。
溶接電流により、Bだけでなく、AやCでも発熱しますが、直流を利用するスポット溶接機では、電極の極性と金属種によりAで発熱・Cで吸熱する場合と、Cで発熱・Aで吸熱する場合が存在します。(交流溶接機では、極性が反転するため相殺されます。)
Aで吸熱の場合、上の電極は、ペルチェ効果により冷却されるので溶着しにくくなりますが、下の電極は逆にペルチェ効果による発熱のために溶着しやすくなります。
このためY材の融点が低い場合などは、下側となる電極の放熱に配慮することが必要になります。
下側の電極に棒状電極(写真)を使用することでY材の電極がわの温度は上がりにくくなります。 |
|
いろいろな抵抗溶接 |
スポット溶接は、溶接する材料に電気を流してその抵抗で発生した熱(ジュール熱)で金属を溶かして接合するため抵抗溶接の一種に分類されます。 スポットはその名の通り「点」なので、連続して線状に溶接する場合は、シーム溶接と呼んでいます。 |
電源による分類 |
溶接機では、商用電源(100Vまたは200V)に接続して、溶接電極に大電流を供給する装置
そのものを「電源」と称しています。
(1)交流式・・・トランスを用いて電極に交流(50Hz又は60Hz)を
加えます。
通電時間はサイクル数で表します。50Hzの場合、最短1サイクルは20ミリ秒です。
大電流を流すことのできる太い巻き線を備えた大きく重いトランスが必要です。
(2)直流式・・・電極に直流を加えます。大電流を必要な時間だけ流せる電源が
必要になります。通電時間は秒で表します。
(3)コンデンサ式・・・コンデンサに蓄え電極に通電します。
時間をかけてコンデンサに
充電できるため、電球1個分程度の商用電源で動作させることができます。 |
ワークの形状・加圧方法などによる分類 |
突合わせ溶接(upset Welding) は金属の木口(端面)同士を突合わせて溶接するのですが、その中に電流の流し方や圧力の加え方などによってバッド溶接 やフラッシュバッド溶接と呼ばれる溶接方法があります。 突き合わせ溶接をする際に、突き合わせ部分の切り口を意図的に突起を残すことにより、プロジェクション溶接を要素取り入れ、溶接強度を上げることもできます。
バッド溶接(butt welding)は、突合わせた部分に圧力を加えながら通電して発熱・溶接します。この際(スポット溶接の中では比較的長時間加熱するため)、軸方向に圧縮して長さを短くし断面が大きくなる「据え込み」が発生します。そのため溶接後に据え込み部分をグラインダーで整形する必要があります。例としては、工事現場でバンドソー(帯鋸)を溶接するための
可搬型バッド溶接機があります。アプセット(upset welding)溶接とも呼びます。
フラッシュ溶接は、溶接初期段階では大きな圧力は加えず、電気抵抗による発熱のほかに、発生するアーク放電を積極的に利用して加熱し、その後圧力を加えて溶接します。このため制御は難しいのですが比較的高い溶接強度が得られます。
プロジェクション溶接は、板材同士を溶接する時に、一方の板材にあらかじめ突起加工を施し、ここにスポット溶接の電極をあてがって溶接する方法です。突起部に熱集中させるにより軟化、圧着が進むとスポットは拡大し電流密度は低下ていきます。しかし、温度上昇により電気抵抗は増加しているため発熱しやすい状態が保たれ、突起を設けない場合に比べて良質な溶接部分(ナゲット)が得られます。問題点としては電流・圧力・通電時間という抵抗溶接の条件に加えて”突起部の作り方”が関係してくるため、溶接の条件設定はより厳しいものになります。
クロスワイヤ溶接は、クロスさせた状態でワイヤ(線材)を溶接する際に溶接部分の形状がプロジェクション溶接の一種と考えられる理想的な形になるためにそう呼ばれています。ただ1点だけで接触した状態で通電が始まりプロジェクション溶接が進行します。
スタッド溶接は、ボルトやナットなどのピンを、平板などの部材に溶接する方法です。
<クリックでビデオ再生(別ウィンドウ・音あり)>
|
【スポット溶接】
部材重ねた部分に、電極を押し当て通電すると、電流により電極に挟まれた部分が発熱します。同時に電極には圧力を加えますので、発熱し溶けた金属同士が接合します。これがスポット溶接です。スポット溶接では 電流・通電時間・圧力の3つが重要な要素となります。
【据え込み(upset)について】
突合せ溶接では、加える圧力にもよりますが、溶接部分に「据え込み」が発生します。据え込み(すえこみ)とは、金属を加熱して曲げたり延ばしたりする鍛造作業における用語の一つで、素材を軸方向に圧縮して長さを短くし断面を大きくする作業のことを指します。つまり、溶接部位が圧力により膨れることを「据え込み」が発生するといいます。
|
電極形状や通電方法よる分類 |
【ダイレクトスポット溶接】
 |
溶接対象物の上下から電極を当てる方法で、最短の電流経路により、理想的なスポット溶接が期待できます。 |
赤(電極)→緑(ワーク1)→橙(ワーク2)→青(電極) |
【インダイレクトスポット溶接】
 |
溶接対象物の上下から電極を当てることができない場合、溶接対象物内の電流経路が長くなりますが、溶接可能です。 |
赤(電極)→緑(ワーク1)→橙(ワーク2)→青(電極) |
 |
バッテリーにタブを溶接する場合のように、ワークの片方に電極を当てることが不可能な場合、2本の電極を同じワーク側から当てることにより溶接します。 |
赤(電極)→緑(ワーク1)→橙(ワーク2)→緑(ワーク1)→青(電極) |
|
この他、接着剤を併用するウェル土ボンドや複数の電極を利用するマルチスポット溶接など多くのスポット溶接が存在します。
同一箇所に対して複数回溶接する場合、パルセーション溶接と呼ぶことがあります。
ミシンで縫うように、連続してスポット溶接を行う方法はシーム溶接と呼ばれています。
データベースには、多くの金属種の詳細事例があります。 Yokodai.JP製溶接機で実際にテスト溶接した結果報告です。
|